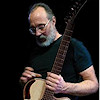 Ken Parker KenParkerArchtops.com
This project began with our local jazz guitar genius, Peter Fedele, and his wonderful 1953 Epiphone Archtop guitar. The top is laminated spruce, and the rail braces (see scary photos!) are poplar. This old archtop has a cool vibe, and a nice history, having been used extensively by Duke Robillard for recording and live performance. It really sounded great, and there were no problems with it except for a terrible built - in shortcoming! Because the fret slots were sloppily cut, and out of position, (some frets even were crooked!), there was no way for the guitar to play in tune in any position on the neck. Peter loved the vibe and provenance of the instrument, and made it sound delicious, but was exhausted and discouraged with trying to play in tune.
Over the years, various repairmen tried every trick in the book to improve the intonation, including installing a tunable, adjustable nut (!) , adding a Gibson style 6 way intonable bridge top, and even screwing the bridge base to the top!
The only real fix was a new fingerboard with correctly placed fret slots.
Because of the large, three part pearl and abalone inlays and the many plastic binding and purfling stripes in this particular fingerboard it looked like a daunting project to a guy like me who does neither of those things in his own work.
Fortunately my friend Brian Galloup at Galloup Guitars encouraged me to let them help with the project! I mailed him the guitar so they could take accurate measurements and see what they could do about making a faithful replica with correct fret slot positioning.
Their capable young team went to work, and It wasn't long before I had a lovely rosewood fingerboard with perfectly executed mother-of-pearl and abalone inlays as well as the goofy original style plastic binding, ready for side dots and frets!
The young geniuses at Galloup decided to faithfully misposition the inlays to match the original fingerboard. Color me thrilled!! Funky old vibe retained!!
When all was back at my workshop, I removed the fretboard with the aid of an old iron and an old-fashioned wedge-shaped table knife.
One issue complicating the removal of the fretboard was the odd placement of the unique truss rod in this guitar, right underneath, and even within the fingerboard!
Before I describe the rest of the rod's miserable features, the innovative feature of this rod was a nicely hot forged 5/32" allen socket for turning the useless rod. Credit where credit is due.
|