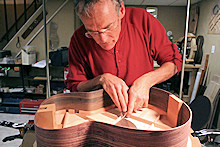 David MacCubbin Guitars www.MacCubbinGuitars.com
Following a lifelong love of woodworking as a hobby, having worked with cabinetry, home construction projects, furniture building and refinishing, David started his lutherie career in 2002, building his first guitar using William Cumpianos and Jonathan Natelson's textbook "Guitarmaking, Tradition and Technology" as a guide. David took the opportunity to study with William Cumpiano in 2003 at his Northampton, Massachusetts shop, where he learned many of the finer points of the craft. Since that time, he has continued to develop his lutherie skills, transitioning from a part-time guitarmaker to full time luthier in early 2007. He has also had the good fortune to be able to attend Ervin Somogyi's guitar voicing master class in 2007, where he gained much greater insight into the relationships among choice of woods, top bracing patterns, construction techniques, and their effects on the resultant sound and response of the guitar. His shop is located in suburban Baltimore, Maryland, where he builds about 10 to 12 guitars a year.
"I installed The D tube into the neck of one of my Sound Investment guitars, and was amazed at the difference it made in the sound production of the instrument. I had two of these guitars on hand, and prior to the D tube installation, both guitars sounded very similar to each other, both in terms of volume and clarity/quality of sound. After installing the D tube, the modified guitar had a significant increase in volume, as well as more clarity and crispness to the notes, providing a remarkable enhancement to the sound production of the instrument. These improvements were apparent throughout the range of the guitar, from bass to treble.
To me, this provides a clear indication of just how much the guitar neck contributes to the overall sound of the guitar, and that a lighter, stiffer neck improves the guitar�s responsiveness significantly. I plan to continue using the D tube on future instruments."
David MacCubbin
|
I first removed the bolt-on neck from the guitar.
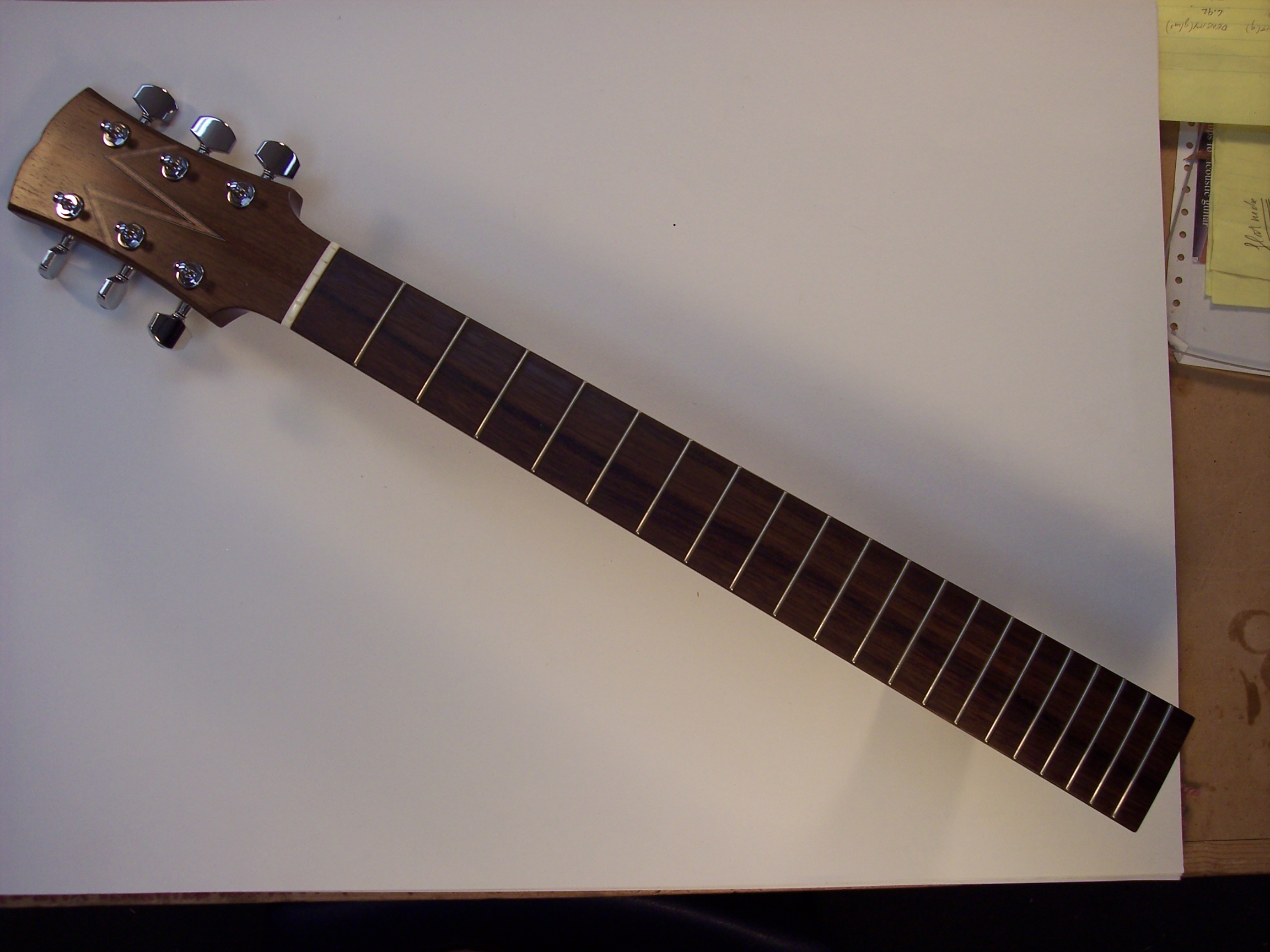 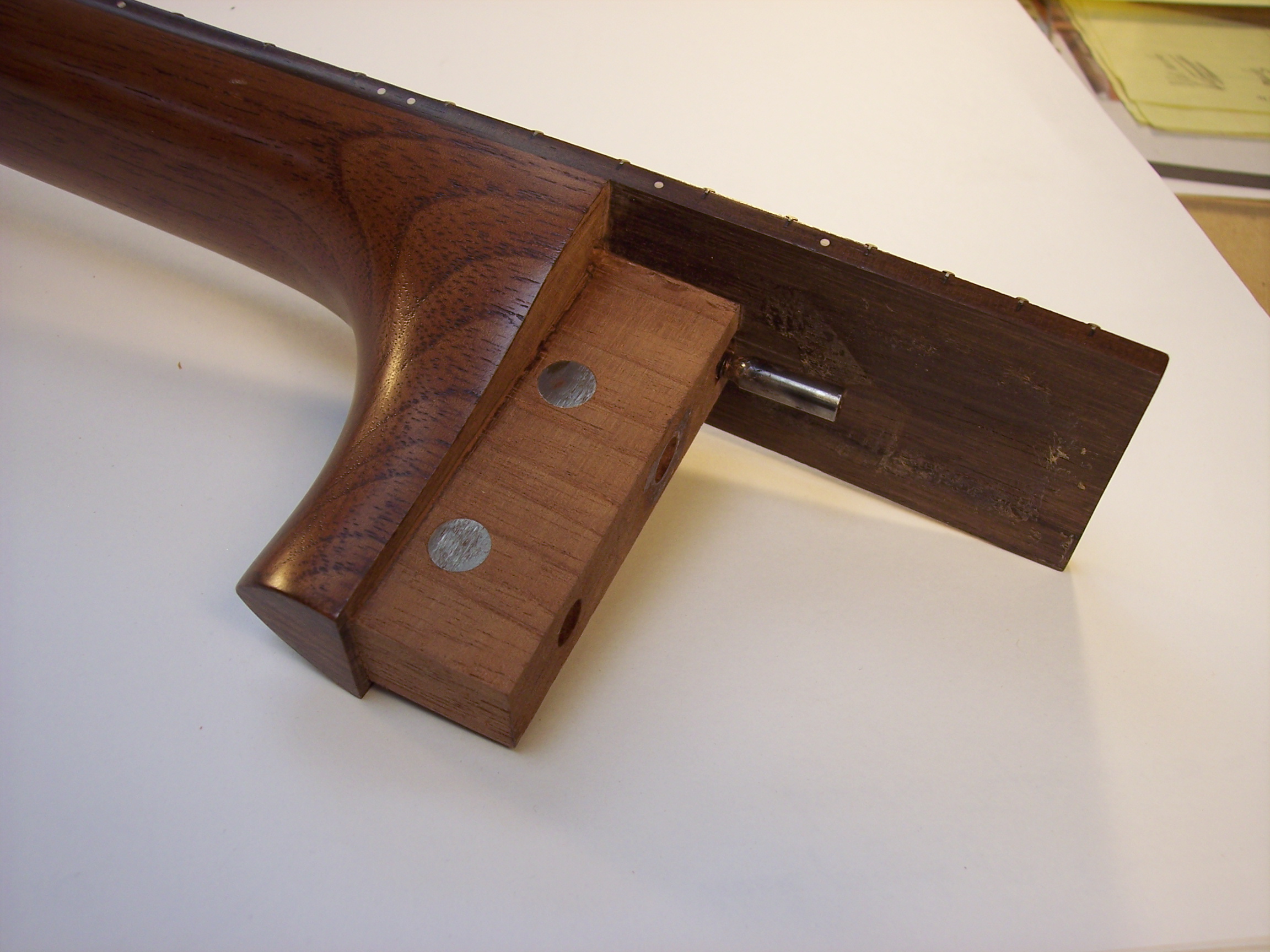
The neck had a two-way truss rod installed, as well as two rectangular carbon fiber rods on either side of the truss rod. To ensure the fit of the D tube in the guitar neck I drew a full scale diagram of the cross section of the neck at the first fret with the D tube.
I then removed frets 1 and 13 and drilled locater pin holes through the fret slots into the neck, gluing the fretboard back in place.
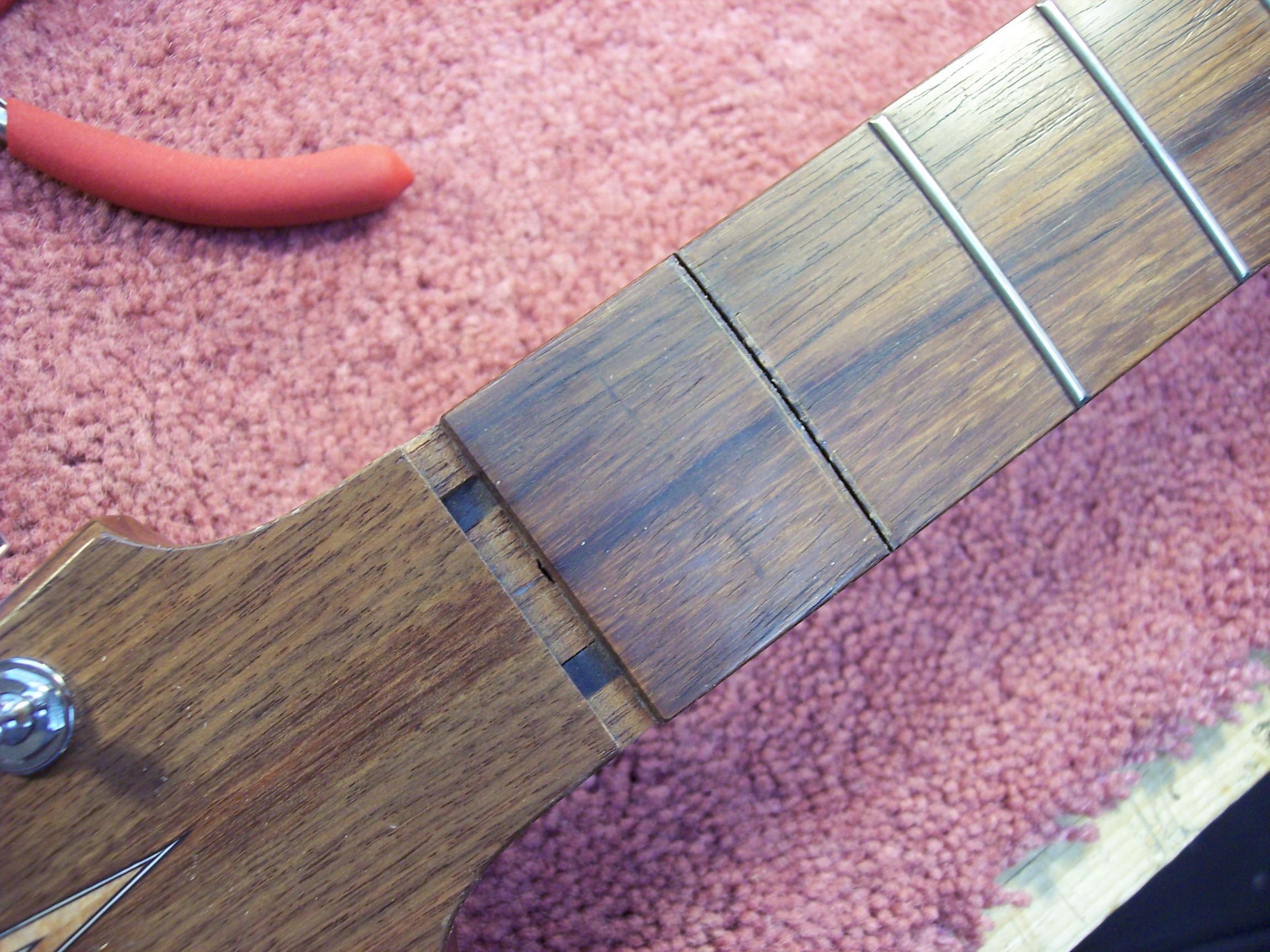 
Using a heating blanket, I removed the fretboard from the neck, allowing the truss rod to be removed and the neck and fretboard surfaces to be cleaned of glue residue.
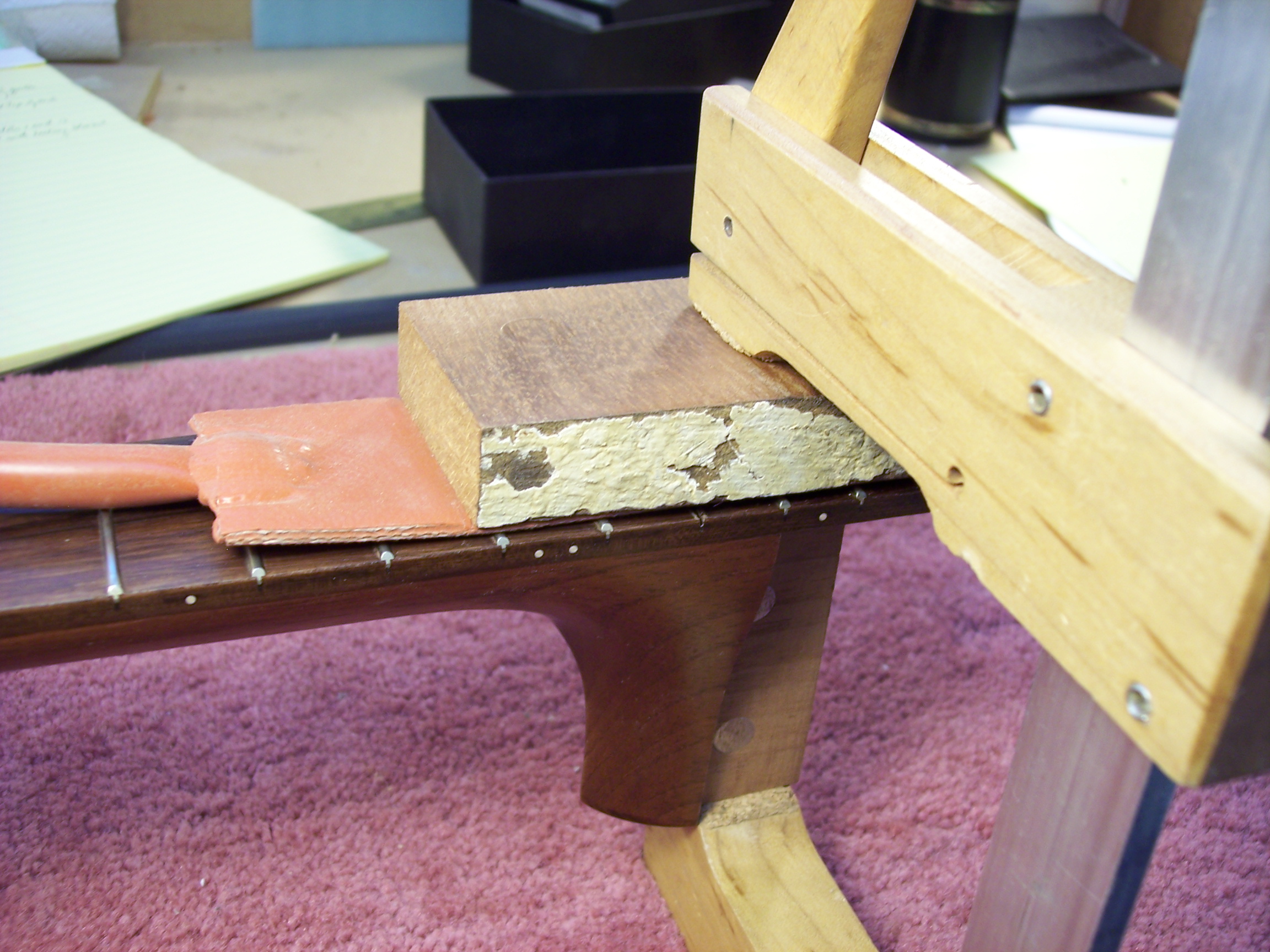 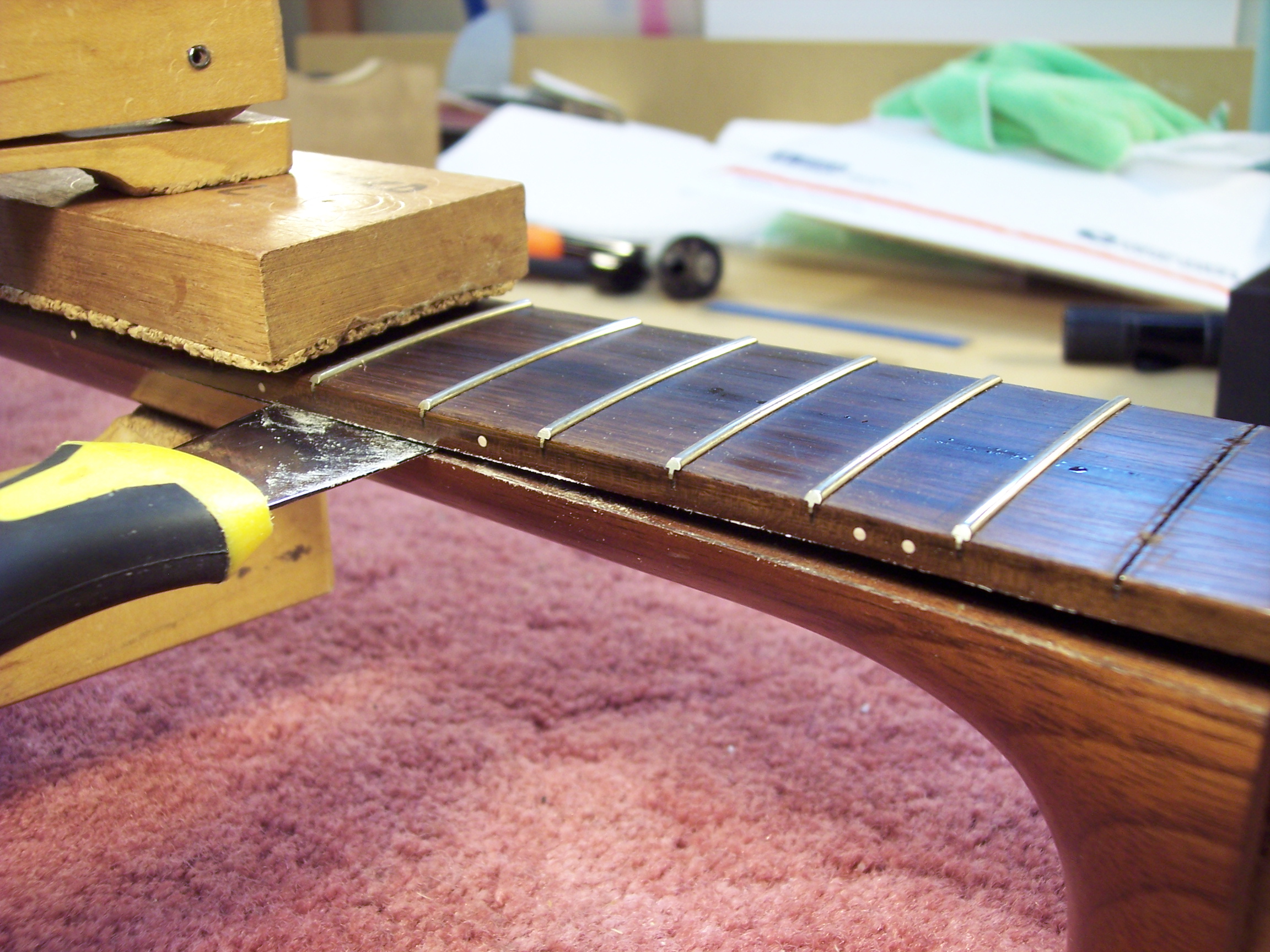
Since the neck is tapered from the extension to the nut, and the rout for the D tube needed to be centered, I constructed a taper jig which allowed routing parallel to the center of the neck.

I first routed a .050 inch pocket into the neck for the mahogany spline that would cover the D tube and provide a smooth surface for re-gluing the fretboard.
Using a .75 core box router bit, I then routed the channel for the D tube from the heel to the nut.
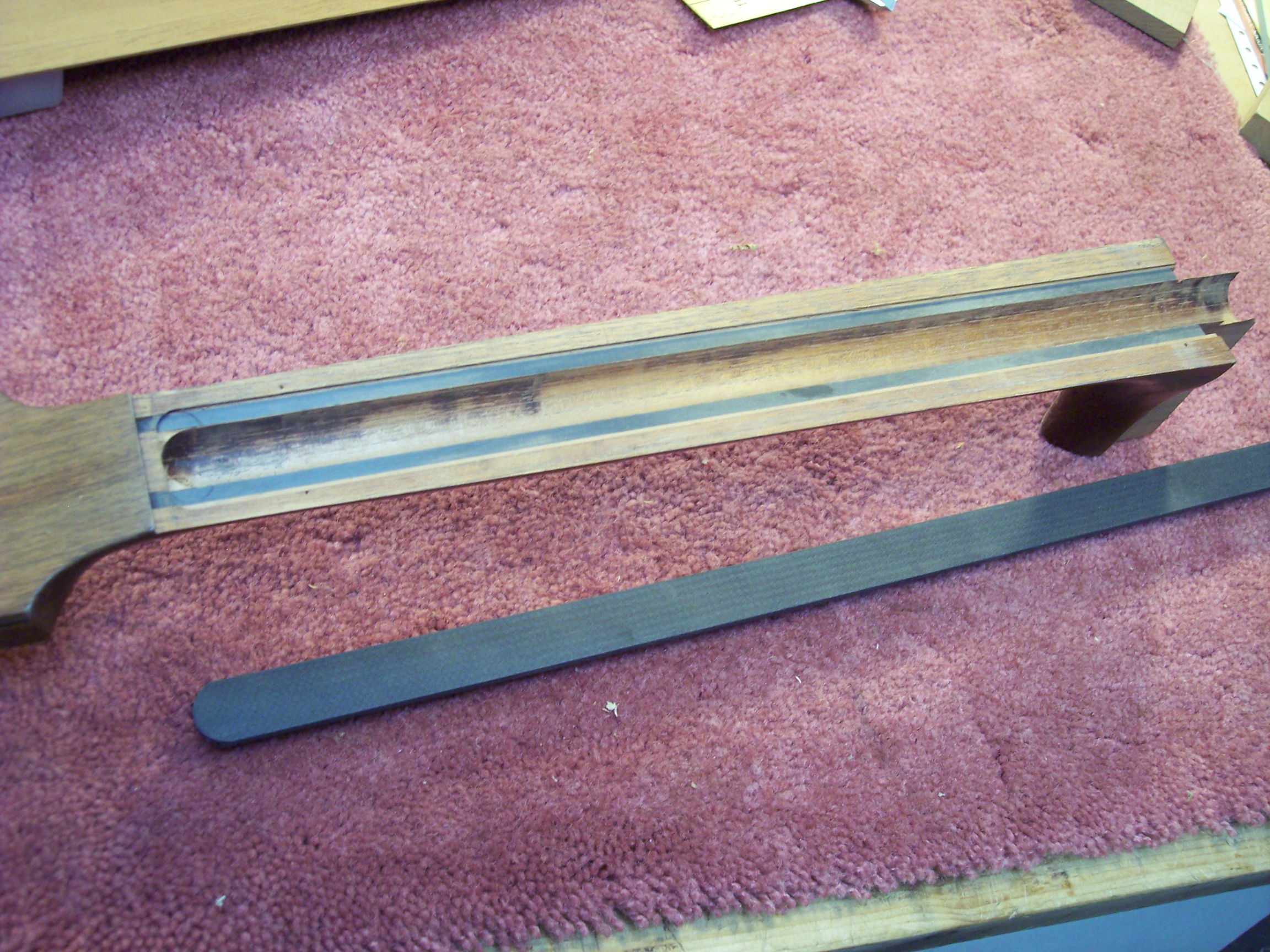
With a grinder, I shaped the end of the D tube to fit the end of the channel at the nut.
I cut the excess overhang off at the end of the heel tenon with a Dremel cut-off wheel.
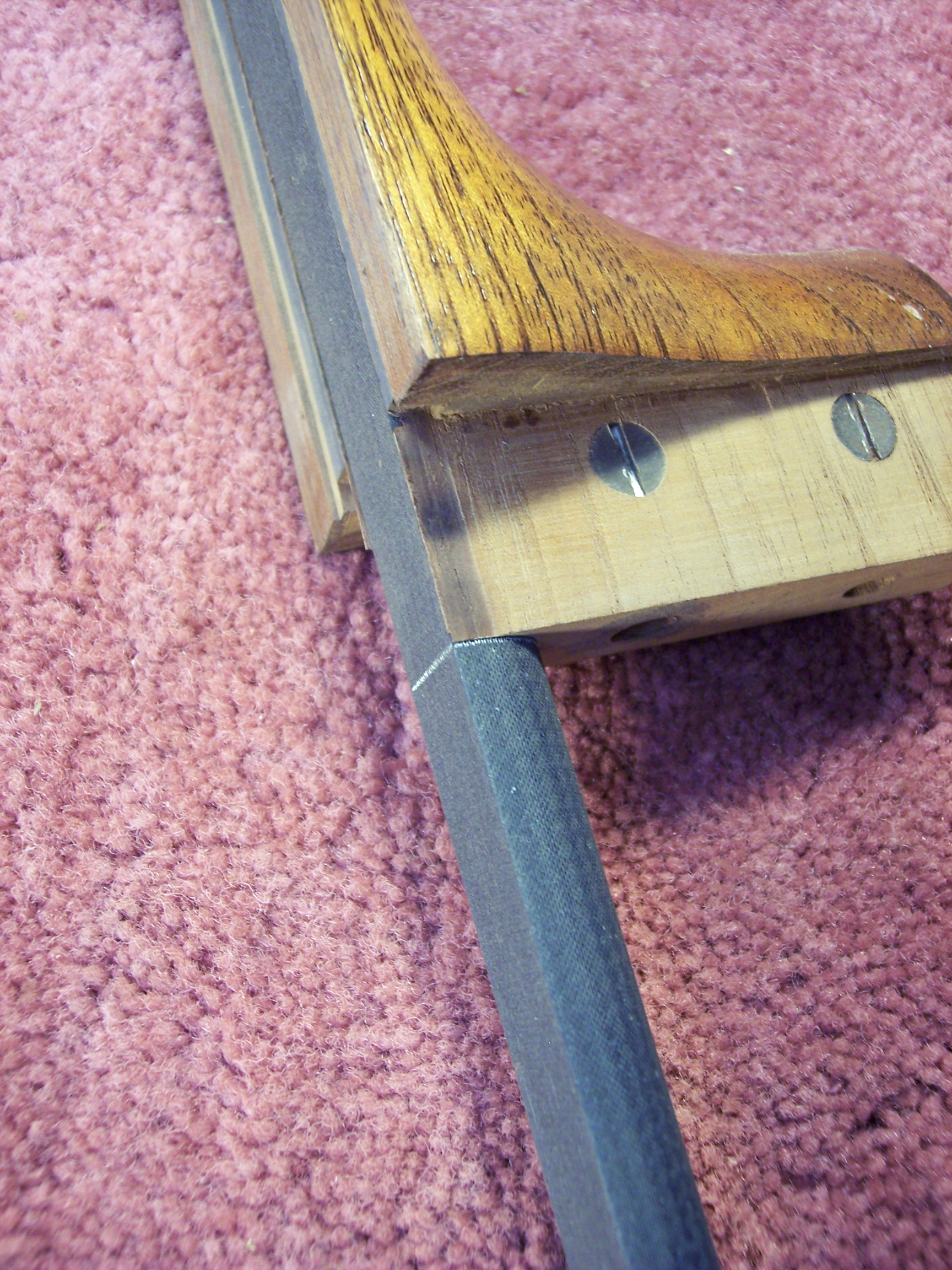
I then cut and fit a mahogany spline to cover the D tube, gluing both in place with West Systems marine epoxy, and scraping/sanding the spline flush with the top of the neck, to achieve a flat surface.
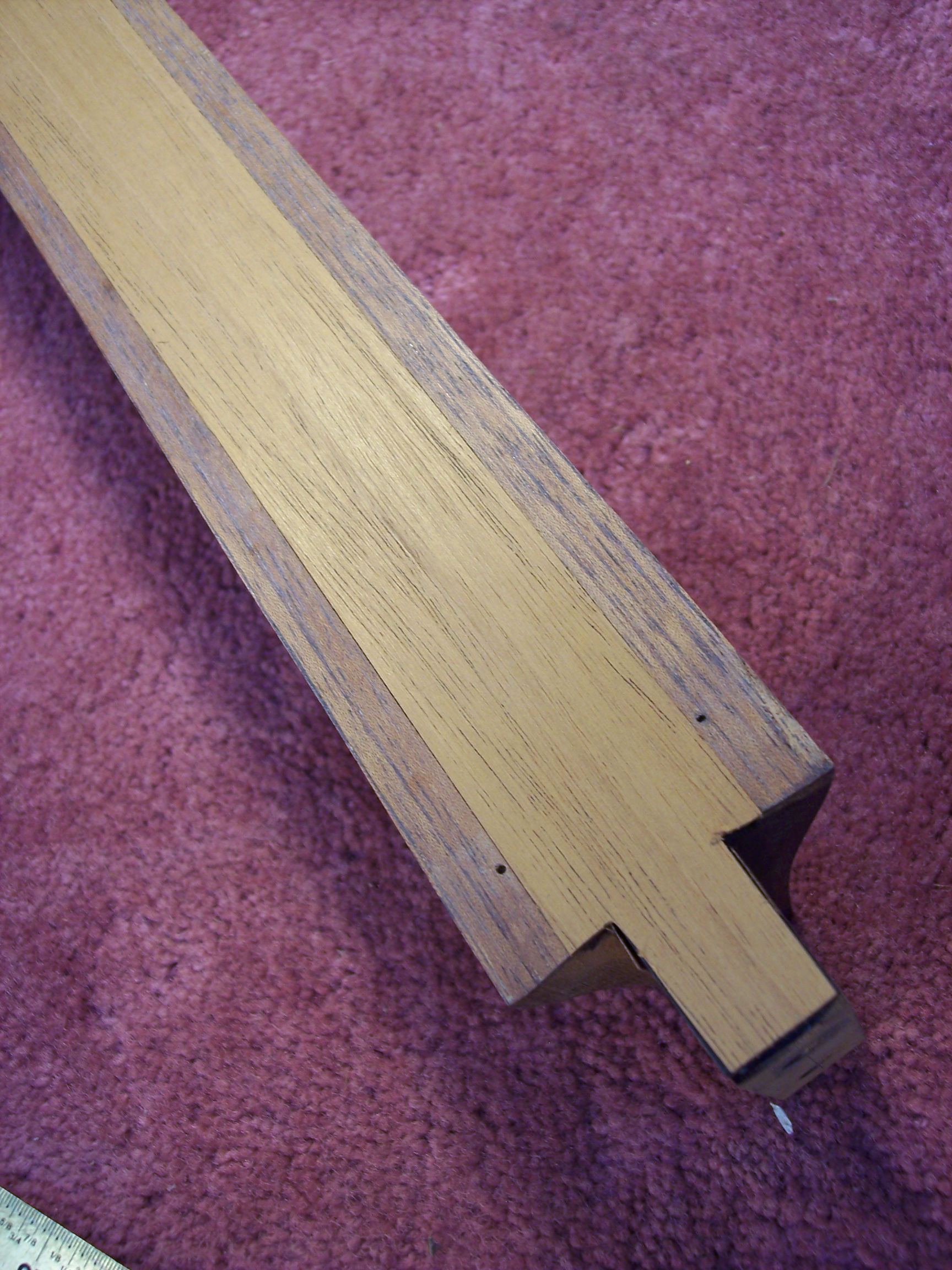 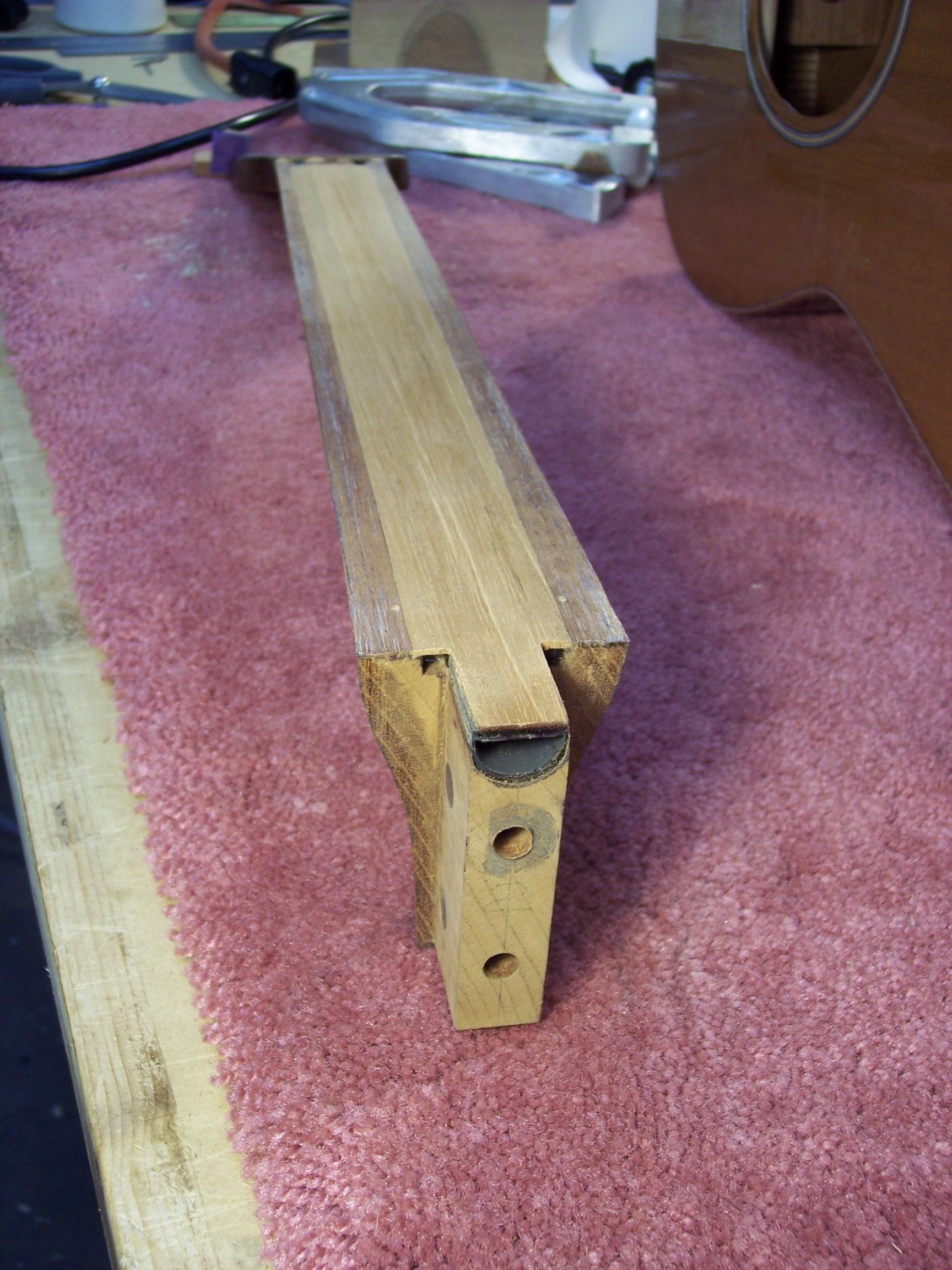
Finally, I re-glued the fretboard onto the neck, using the locator pins to ensure the correct location.
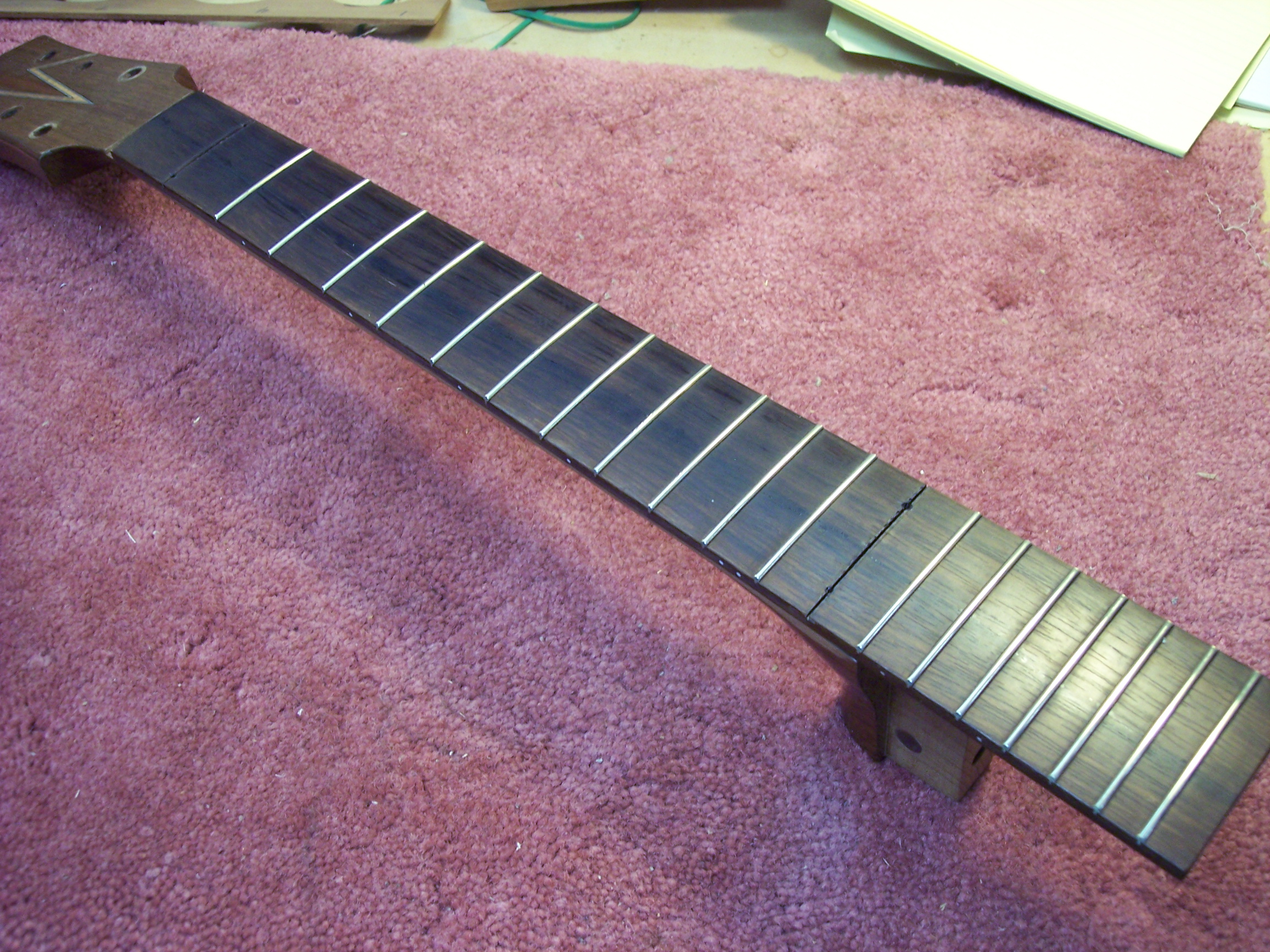
I reinstalled the neck onto the guitar, and once the missing frets were replaced, the frets leveled and setup done, I restrung the guitar. There was a noticeable difference in volume and clarity after the D tube installation. The guitar is definitely more responsive, louder, and the tones are more clearly defined across the spectrum from highs to lows.
|